Cryogenic labels play a critical role in laboratories, biobanks, and pharmaceutical storage, where samples must remain securely identified at ultra-low temperatures. Standard labels fail in extreme cold, leading to adhesive failure, barcode degradation, and lost samples, making specialized cryogenic labeling solutions essential. A well-engineered cryogenic label must withstand liquid nitrogen (-196°C), deep freezers (-80°C), dry ice, and exposure to cryoprotectants without peeling, smearing, or losing readability. Selecting the right face stock, adhesive, liner, and protective coatings ensures long-term durability and reliable sample tracking. Additionally, understanding the difference between application and operating temperatures is crucial for preventing adhesion failures that compromise sample integrity. This guide explores the key materials and technologies behind cryogenic labels, helping laboratories choose the best labeling solutions for extreme cold storage applications.
Understanding cryogenic label requirements.
Cryogenic labels must perform under some of the most extreme conditions in laboratory and biobank environments. Unlike standard labels, which may only need to resist moisture or mild temperature fluctuations, cryogenic labels are exposed to ultra-low temperatures, rapid freeze-thaw cycles, and harsh chemicals such as liquid nitrogen and cryoprotectants. If a label fails—whether by detaching, smearing, or becoming brittle—critical samples can become untraceable, leading to lost research or compromised medical materials. Cryogenic labels must be engineered to prevent these failures with precise material properties that ensure durability, readability, and adhesion in extreme cold. Below are the essential performance characteristics that define a reliable cryogenic labeling solution.
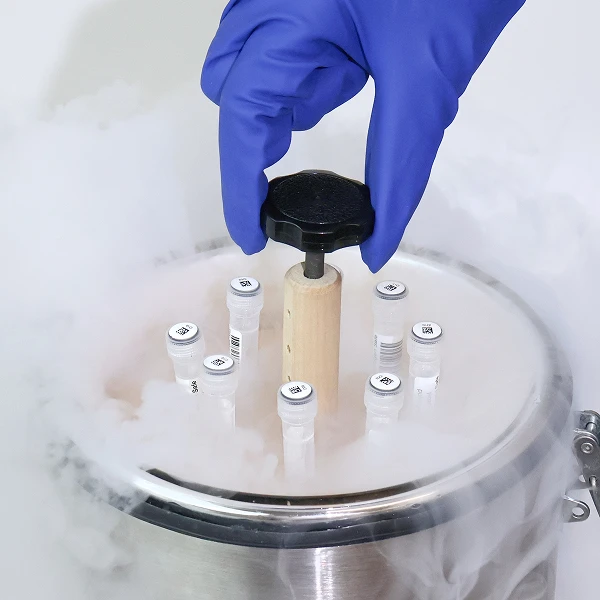
Thermal Resistance & Stability
Cryogenic labels must withstand ultra-low temperatures without degrading, peeling, or becoming brittle. While many materials maintain their integrity in cold storage (-20°C to -80°C), cryogenic applications often require stability at temperatures as low as -196°C in liquid nitrogen storage. Standard adhesives and face stocks often become rigid or lose adhesion due to thermal contraction in these conditions. Cryo-optimized materials must exhibit low shrinkage and high mechanical strength, ensuring the label remains intact and legible throughout long-term storage.
Moisture Resistance & Barrier Coatings
Cryogenic labels frequently encounter humidity, condensation, and frost formation when samples are transferred between storage and ambient conditions. If a label absorbs moisture, the adhesive can weaken, the face stock may degrade, and printed information can smudge or fade. Materials must have hydrophobic properties or be treated with barrier coatings to prevent water penetration. Additionally, some labels use self-laminating films that seal and protect printed data from exposure to moisture and ice buildup.
Dimensional Stability & Shrinkage Control
At extreme temperatures, materials contract and expand. If a label’s dimensional stability is poor, it may warp, lift, or detach from the sample surface. Polyester (PET) labels excel in dimensional stability, resisting temperature-induced shrinkage better than polyethylene or polypropylene. This property is critical for ensuring that barcodes and text remain readable and that automated sample tracking systems can accurately scan labels without distortion.
Chemical Resistance & Solvent Durability
Cryogenic samples are often stored in liquid nitrogen, dry ice, or cryoprotective solutions such as DMSO and ethanol, all of which can degrade standard labels. A cryogenic label must resist chemical breakdown, ensuring that the adhesive remains intact and that printed information does not fade or dissolve upon exposure. Polyester face stocks and acrylic-based adhesives are particularly well-suited for these conditions, providing superior resistance to harsh lab chemicals.
Shear Strength & Peel Strength for Secure Bonding
Adhesion failure is one of the biggest risks in cryogenic environments. Labels must have high shear strength to prevent sliding or slipping when exposed to handling and shifting temperatures. Peel strength is also critical, ensuring that the label remains securely bonded to tubes, vials, or plates even under extreme cold. Some adhesives are formulated with tackifiers and stabilizers that improve their bonding capability across different surfaces, including low-energy plastics like polypropylene and polyethylene labware.
Print Durability & Abrasion Resistance
A label’s printed information must remain scannable and legible for the entire lifespan of the sample. Cryogenic storage often involves handling, friction, and exposure to ice crystals, all of which can wear down printed barcodes and text. Face stocks with abrasion-resistant coatings or self-laminating overlays provide an additional layer of protection against physical damage. Thermal transfer printing with resin ribbons is often recommended for cryo labels because resin-based prints chemically bond to the label surface, creating a durable, chemical-resistant image.
Each of these characteristics plays a role in ensuring that cryogenic labels remain secure, scannable, and stable throughout their use. When selecting a cryo label, labs must consider not just the storage temperature, but also the entire lifecycle of the sample, from printing and application to long-term retrieval. In the next section, we’ll take a closer look at the materials used in cryogenic face stocks, explaining why some materials outperform others in ultra-low-temperature environments.
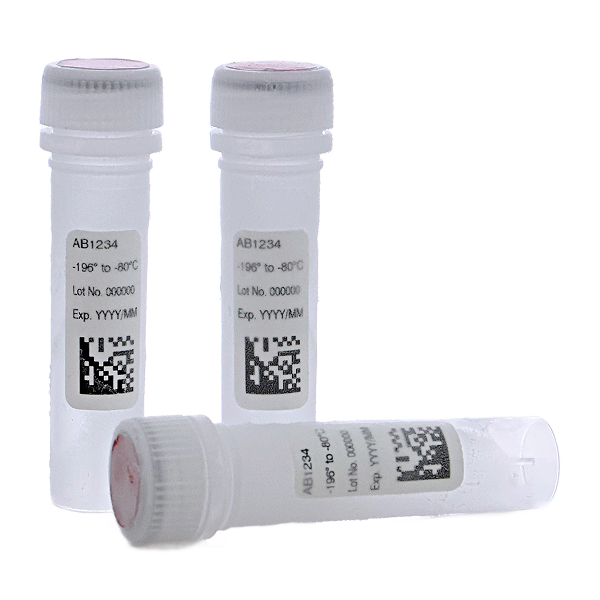
Cryogenic adhesives: engineered bonding for subzero environments.
In cryogenic storage, choosing the right face stock is only half the battle—without the right adhesive, even the best label material will fail. Cryogenic environments present significant challenges for adhesion, including thermal contraction, moisture exposure, and chemical interactions with liquid nitrogen, ethanol, and other solvents. General-purpose adhesives often become brittle, lose tack, or detach entirely in extreme cold, making it critical to use adhesives specifically designed to maintain bond strength at ultra-low temperatures. A well-engineered cryogenic adhesive must offer high initial tack, long-term adhesion, and chemical resilience to ensure labels stay securely affixed to tubes, vials, and plates throughout the sample’s lifecycle.
Essential Characteristics of Cryogenic Adhesives
Cryogenic adhesives must be formulated to withstand temperature extremes, chemical exposure, and environmental stressors without losing performance. The following characteristics define an effective adhesive for subzero applications:
- Thermal Resistance & Low Cold Flow
At temperatures below -80°C, many adhesives become brittle and lose adhesion, leading to peeling, edge lift, or complete failure. Cryogenic adhesives must be designed with low cold flow, meaning they do not become too rigid or ooze under extreme conditions. Acrylic-based adhesives generally outperform rubber-based adhesives in extreme cold because they maintain their bond without excessive hardening or flow. - High Initial Tack & Shear Strength
Labels applied to cryogenic samples must bond quickly since many are affixed immediately before freezing. High initial tack ensures that the adhesive grabs the surface even at low application temperatures, while shear strength prevents movement or slipping over time. This is particularly important for automated sample processing, where labels need to stay precisely in place on tubes and vials. - Excellent Wet-Out Properties & Surface Energy Adaptability
Many labware surfaces, including polypropylene and polyethylene tubes, have low surface energy, making them difficult for standard adhesives to bond to. Cryogenic adhesives must have enhanced wet-out properties, meaning they can spread evenly across the surface, maximizing adhesion strength. Tackifiers or specialized coatings may be used to improve adhesion to challenging materials. - Oxidation Resistance & Chemical Stability
Cryogenic samples are often stored in liquid nitrogen (-196°C), dry ice (-78.5°C), or solvents like ethanol and DMSO, which can degrade adhesives over time. Cryogenic adhesives must be formulated to resist oxidation and chemical interactions, preventing bond failure, discoloration, or weakening due to prolonged exposure. - Plasticizer & Solvent Resistance
Some plastics used in labware contain plasticizers, which can migrate into adhesives and weaken bonds over time. Cryogenic adhesives must be plasticizer-resistant to prevent softening, lifting, or detachment. Additionally, they must withstand solvents used in lab environments, ensuring labels remain intact despite exposure to harsh chemicals.
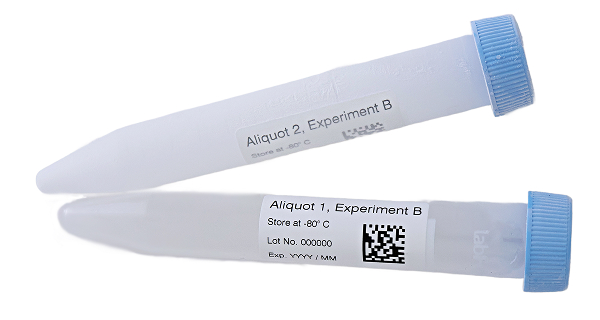
Comparing Cryogenic Adhesive Types
Not all adhesives perform equally in cryogenic environments. While rubber-based adhesives offer strong initial tack, they can lose flexibility at extreme temperatures. Acrylic adhesives, on the other hand, are designed for long-term stability in ultra-low temperatures, making them the preferred choice for cryogenic labeling. Custom adhesive formulations can further optimize performance for specific applications.
- Acrylic Adhesives – The Cryo-Optimized Standard
Acrylic adhesives are the most reliable option for long-term cryogenic storage. They maintain strong adhesion, resist chemical degradation, and perform well at temperatures as low as -196°C. Acrylic adhesives also bond effectively to a variety of surfaces, including low-energy plastics like polypropylene and polyethylene, making them an excellent choice for labware labels.
- Long-term cryogenic stability
- Resists extreme cold (-196°C)
- Bonds to low-energy plastics
- Excellent chemical resistance
- Good wet-out properties
- High shear strength
- Rubber-Based Adhesives – High Tack, but Limited Cryo Stability
Rubber adhesives provide quick initial adhesion and work well in cold storage (-20°C to -80°C), but they are not ideal for deep cryogenic storage. They tend to harden, lose flexibility, and weaken over time when exposed to liquid nitrogen or cryogenic solvents. However, they can still be effective in freezer applications where rapid adhesion is needed.
- Fast initial adhesion
- Strong tack on rough surfaces
- Performs well in freezer storage
- Limited cryogenic performance
- Can become brittle over time
- Custom Adhesives – Tailored for Extreme Applications
For highly specialized cryogenic applications, custom adhesives can be formulated with additives that enhance specific performance characteristics. By modifying base adhesives with stabilizers, tackifiers, and rheology modifiers, engineers can create solutions optimized for unique surfaces, handling requirements, and environmental conditions.
Common Additives in Custom Cryogenic Adhesives
- Tackifiers – Improving Initial Adhesion
Tackifiers are added to adhesives to increase initial tack, helping labels bond quickly even at low application temperatures. This is particularly useful when labels are applied to cold, low-energy plastics that are difficult to adhere to without specialized formulations. - Stabilizers – Enhancing Chemical and UV Resistance
Stabilizers prevent adhesive breakdown due to oxidation, UV exposure, or chemical interactions. This is especially important for labels stored in transparent cryo vials, which may be exposed to light and chemicals over extended periods. - Cold Flow & Shear Strength Adjustments
Adjusting cold flow properties ensures that adhesives remain stable at ultra-low temperatures, preventing excessive spreading or stiffening. High shear strength adjustments help labels stay securely in place, preventing shifting or peeling during freeze-thaw cycles.
- Tackifiers – Improving Initial Adhesion
Engineering Cryogenic Adhesion for Long-Term Stability
The right adhesive is just as important as the right face stock when designing a cryogenic label. Acrylic adhesives offer the best all-around performance for ultra-low temperatures, while rubber-based adhesives are better suited for freezer storage applications. Custom adhesive formulations can be designed to address specific bonding challenges, ensuring labels remain intact and readable throughout the sample’s lifecycle.

Cryogenic face stocks: durable, flexible substrates for cold storage labeling.
Choosing the right face stock is one of the most critical decisions when designing a cryogenic label. The face stock determines durability, print quality, flexibility, and resistance to environmental factors such as moisture and extreme cold. Unlike standard labels, which may only require basic resistance to handling and temperature shifts, cryogenic labels must endure prolonged storage in liquid nitrogen (-196°C), dry ice (-78.5°C), and deep freezers (-80°C) without warping, peeling, or losing readability. Selecting the wrong material can result in brittle labels, damaged barcodes, or complete adhesion failure, making material selection essential for ensuring long-term sample traceability in biobanks, pharmaceutical labs, and research facilities.
Not all label materials perform equally in cryogenic storage. Some offer exceptional durability and print stability, while others are better suited for flexible or temporary applications. Below is a comparison of the most common face stocks used in cryogenic labels, outlining their key strengths and limitations.
Polyester (PET)
Polyester is commonly used for cryogenic labels due to its dimensional stability, thermal resistance, and chemical durability. It maintains shape, adhesion, and print clarity even after long-term exposure to liquid nitrogen (-196°C) and harsh chemicals. While PET is rigid and less conformable than polyethylene, it is ideal for flat and semi-rigid surfaces where labels must remain secure for years.
- Extreme temperature stability
- High tensile strength
- Superior chemical resistance
- Dimensional stability
- Abrasion-resistant surface
Polyethylene (PE)
Polyethylene is highly flexible and impact-resistant, making it a strong choice for curved or irregular surfaces like cryo vials and tubes. While it does not have the same thermal stability as polyester, it performs well in deep freeze and dry ice environments. PE’s flexibility makes it a great option when conformability and durability are required.
- Highly flexible material
- Good impact resistance
- Resistant to condensation
- Performs well in deep freeze
Polypropylene (PP)
Polypropylene is commonly used for general freezer applications but is less suited for cryogenic storage than PET or PE. It offers good moisture resistance and print quality, but it can become brittle in extreme cold. PP is an economical choice for short-term frozen storage but may not be reliable for long-term cryogenic applications.
- Good moisture resistance
- Affordable option
- Stable in mild cold storage
- Compatible with curved surfaces
Selecting the Right Face Stock for Cryogenic Success
Each of these materials has its advantages, but selecting the right one depends on storage conditions, handling processes, and label longevity requirements. Polyester is the top choice for long-term cryogenic storage, offering the best thermal and chemical resistance. Polyethylene is ideal for curved surfaces and moderate cold storage, while polypropylene works for general frozen storage but lacks true cryogenic resilience.
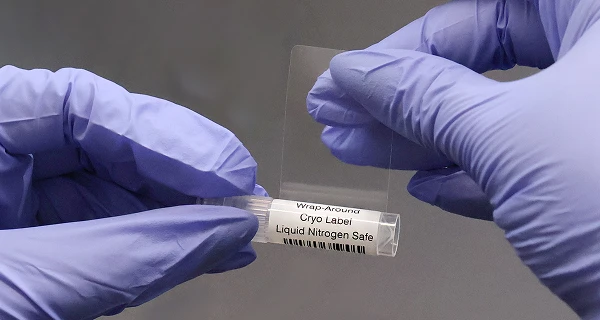
The role of coatings and laminates in cryogenic labels.
While selecting the right face stock and adhesive is essential for cryogenic labels, coatings and laminates provide an extra layer of protection that ensures print durability, chemical resistance, and long-term readability. Without proper protective measures, labels can fade, smudge, or degrade due to exposure to condensation, liquid nitrogen, cryogenic solvents, and physical abrasion during storage and handling. Coatings and laminates serve to enhance label performance by creating barriers against these environmental stressors, ensuring that barcodes and text remain scannable and intact throughout the sample’s lifecycle.
Pre-Coats & Top Coats: Enhancing Print Durability and Adhesion
Pre-coats and top coats play an important role in improving both adhesion and print performance in cryogenic applications. Pre-coats are applied to the label face stock before printing and serve to enhance ink receptivity, improve chemical resistance, and create a smoother surface for thermal transfer printing. This ensures that resin-based thermal transfer ribbons can properly bond with the label, resulting in a highly durable and scannable print that resists smearing and fading over time.
Top coats, on the other hand, act as a protective layer that shields printed information from abrasion, frost buildup, and chemical exposure. Labels in cryogenic storage are often rubbed against each other or handled with gloved hands, increasing the risk of print degradation. A properly formulated top coat adds an extra layer of durability, ensuring that the printed information remains intact even after repeated handling, thawing, and refreezing cycles. For cryogenic applications, top coats must also be engineered to maintain flexibility at ultra-low temperatures, preventing cracking or delamination.
Self-Laminating Labels: Protecting Printed Data in Harsh Conditions
Self-laminating labels are a highly effective solution for protecting printed information in cryogenic storage, particularly for barcodes and variable data that must remain scannable over extended periods. These labels feature a clear laminate layer that is applied over the printed section, creating a sealed barrier against moisture, chemicals, and abrasion. The laminate prevents frost and condensation from distorting barcodes or smudging ink, ensuring that tracking and identification remain accurate throughout storage and handling.
One of the most common cryogenic self-laminating solutions is wrap-around labels for cryovials. These labels are designed to be wrapped around small-diameter tubes and vials, with the transparent laminate portion covering and sealing the printed text and barcode. This design is particularly useful for biobanks, pharmaceutical research, and genetic labs, where cryovials must be stored in liquid nitrogen or deep freezers for extended periods. By using self-laminating, wrap-around labels, labs can ensure that frost buildup and chemical exposure do not compromise critical sample identification.
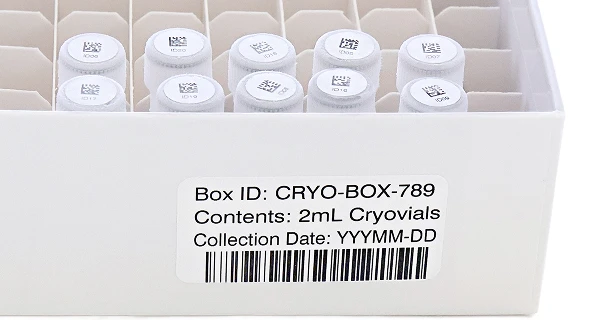
Cryogenic labels must resist not just extreme cold, but also the physical wear and tear that occurs in lab environments. Barrier coatings provide an added layer of protection against chemical exposure, moisture absorption, and mechanical abrasion, helping to extend the life of the label and maintain print clarity. These coatings are especially useful when labels are exposed to repeated handling, freeze-thaw cycles, or direct contact with frozen surfaces.
In high-throughput lab environments, labels can rub against racks, gloves, and lab tools, leading to scratches, smudging, or even partial label detachment if the face stock is not properly coated. Barrier coatings help to minimize these risks by forming a protective film that keeps the label surface intact. Some coatings are also designed to repel condensation, preventing water buildup from interfering with barcode scanning.
By integrating pre-coats, top coats, self-laminating layers, and barrier coatings, cryogenic labels can withstand extreme cold, moisture exposure, and physical wear without losing adhesion or readability. These protective elements ensure that barcodes remain scannable, printed data stays legible, and labels maintain their integrity throughout long-term storage and handling.
Release liners: why they matter for cryogenic labels.
The liner is often overlooked in cryogenic label design, but it plays a crucial role in ensuring smooth application and adhesive performance. In high-throughput lab environments, where thousands of vials or tubes need labeling, the choice of liner can determine whether labels are applied efficiently by automation or require manual placement. Film liners are typically preferred for automated application systems because they provide consistent release properties, reduced static buildup, and higher dimensional stability, allowing labels to be dispensed quickly and accurately. Paper liners, while more cost-effective, can be prone to breakage, curling, or inconsistent label release, making them more suited for hand-applied labeling processes rather than high-speed automation. Additionally, the liner must be engineered to function properly in cold environments, ensuring that the adhesive remains stable and ready for application without premature release or adhesion failure. In automated labeling systems, a smooth, controlled release from the liner ensures proper label placement, preventing misalignment, air bubbles, or label flagging, which could lead to scanning errors or sample misidentification. The right liner selection improves efficiency, reduces labeling errors, and ensures seamless integration into automated cryogenic workflows, making it a critical component of cryogenic labeling success.
Application temperature vs. operating temperature: a critical distinction.
One of the most overlooked factors in cryogenic labeling is the difference between application temperature and operating temperature, yet this distinction is critical to ensuring labels perform as expected in extreme environments.
The application temperature is the temperature at which the label is applied to the surface. If the adhesive is not formulated to bond properly at the application temperature, it may fail to adhere securely, resulting in peeling or detachment when the sample is moved into storage. Many adhesives require a minimum application temperature of around 5°C to 10°C, but cryogenic adhesives must be engineered to bond effectively even when applied to frozen surfaces at temperatures as low as -80°C.
The operating temperature, on the other hand, refers to the temperature range in which the label must remain intact and functional after application. A label may be applied at room temperature, but if it is later stored in liquid nitrogen (-196°C) or deep freezers (-80°C), both the adhesive and the face stock must be able to withstand those conditions without losing adhesion, readability, or flexibility.
If a label is not designed with both application and operating temperatures in mind, it may initially seem secure but later fail in storage, compromising sample identification and tracking. The best cryogenic labels are specifically engineered to bond instantly upon application while also maintaining their integrity in extreme cold over long periods of time.
Cryogenic labels are more than just stickers—they are engineered tools for long-term sample traceability in biobanks, research labs, and pharmaceutical storage. Choosing the right combination of face stock, adhesive, coatings, and liners ensures labels remain secure, scannable, and intact even at ultra-low temperatures. Whether you need labels for liquid nitrogen storage, deep freezers, or automated lab processing, our cryogenic labeling solutions are designed for maximum durability and performance. Request a sample today to see how our labels perform in your environment, or shop our selection of cryogenic labels to find the right fit for your application.
Connect with our labelling experts today
Blog article form
Take advantage of our volume discounts for bulk orders. Reach out to us for a personalized quote tailored to your needs.
"*" indicates required fields