Labeling frozen tubes is a frustrating but necessary task in many labs. Whether you’re receiving cryogenic samples from a biobank, merging collections, or replacing a failed label, sometimes you have no choice but to apply a new label to an already frozen tube. The problem? Frost and moisture prevent adhesion, and most cryo labels—while designed for extreme cold storage—still require a warmer application temperature to bond properly. If you’ve ever tried sticking a label onto a frozen tube only to watch it peel off the moment it’s placed back in the freezer, you already know how challenging this can be.
The good news is that labeling frozen tubes is possible—you just need the right process and materials. This guide breaks down why frozen tube labeling is so difficult, what happens when standard labels fail, and the two best solutions for applying a durable, scannable label to a frozen surface. Whether you’re working with -80°C freezers or liquid nitrogen storage, here’s how to ensure your labels stay put and your samples remain traceable.
Why would you need to label frozen tubes?
In many lab environments, relabeling frozen tubes isn’t just a backup plan—it’s a necessary step in sample management. Whether a lab is receiving samples from a biobank, consolidating collections, or preparing for long-term storage, there are plenty of situations where frozen tubes need new labels. The challenge is that these tubes are often already at -80°C or colder, making traditional labeling methods ineffective. Frost and moisture buildup prevent adhesion, and most cryo labels—while designed for extreme cold storage—still need to be applied at warmer temperatures. That means when relabeling frozen tubes, labs need to use a labeling solution that’s specifically designed to bond instantly to frozen surfaces.
Common reasons for labeling frozen tubes
- Receiving samples from a biobank that require lab-specific labeling
- Reorganizing or merging sample collections across different studies
- Updating labels for consistency in long-term tracking systems
- Replacing labels that peeled off, faded, or became unreadable
- Correcting misidentified or improperly labeled samples
For example, a research lab receiving a shipment of frozen specimens from a biobank will often need to apply their own tracking labels before storing the samples in their freezers. Similarly, a clinical study tracking patient samples over time may need to relabel tubes to standardize formatting across different collection sites. Even in cases where the original labels are intact, labs may still need to apply additional barcodes or identification markers to meet internal tracking requirements.
No matter the reason, labeling frozen tubes is a routine challenge in many labs, and it requires more than just choosing the right label—it also demands an understanding of the conditions that make frozen labeling difficult. In the next section, we’ll break down why standard labels fail on frozen tubes and what must be done to ensure secure adhesion in extreme cold.
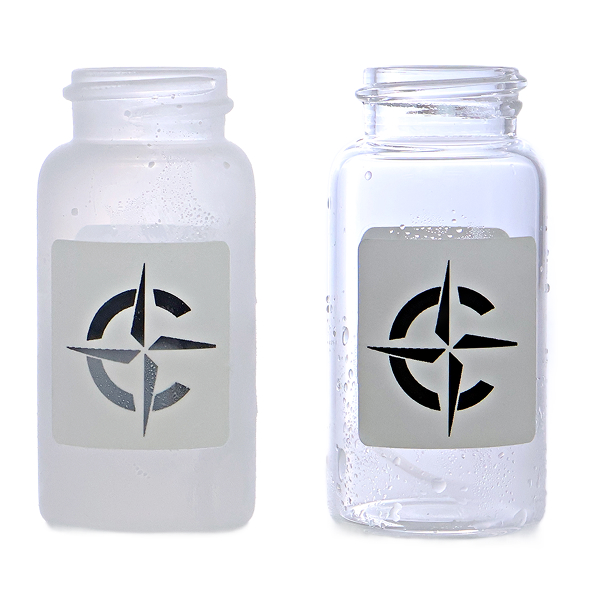
Why is labeling frozen tubes so difficult?
Labeling frozen tubes isn’t just tricky—it’s a fundamental challenge in sample management. Even if a lab has the right cryogenic labels for storage down to -196°C, those labels won’t necessarily bond if applied directly to a frozen tube. The biggest obstacle is moisture—when a tube is at -80°C or colder, it develops an instant layer of frost upon exposure to air. Since nothing sticks to water, this frost completely blocks adhesion, preventing the label from forming a secure bond. Even after wiping the tube dry, if the adhesive isn’t formulated to activate at cryogenic temperatures, it won’t stick, leading to labels peeling off, shifting, or failing entirely once the sample is placed back into storage.
Common problems when labeling frozen tubes
- Frost and moisture buildup prevent adhesion
- Most adhesives require warmer application temperatures
- Labels applied to frozen surfaces peel off when returned to storage
- Freeze-thaw cycles weaken adhesive bonds over time
- Frost can trap air bubbles under the label, reducing contact
The temperature of the tube at the time of application plays a critical role in label performance. Most cryogenic labels are designed for long-term cold storage, but they still need to be applied at warmer temperatures to form a proper bond. This is why understanding application temperature vs. operating temperature is essential for successfully labeling frozen tubes.
Application Temperature: When the Label is Applied
The application temperature is the minimum temperature at which an adhesive can properly bond to a surface. Many cryogenic labels can withstand storage in liquid nitrogen (-196°C) or ultra-low freezers (-80°C), but their adhesives still need to be applied at room temperature or slightly chilled conditions—typically no lower than -20°C to -40°C. If applied to a tube that’s already frozen at -80°C, the adhesive will remain rigid and inactive, preventing a secure bond.
Operating Temperature: The Long-Term Storage Environment
The operating temperature is the temperature range in which the label must remain functional after application. A label may be rated for long-term cryogenic storage, but if it was applied incorrectly—at too low of an application temperature or with frost still on the tube—it may fail in storage despite being designed for extreme cold.
This distinction is crucial because a label that isn’t applied correctly may appear to stick at first but will start peeling off once the sample is placed back into storage. That’s why it’s so important to remove moisture, use an adhesive that bonds at frozen temperatures, and apply labels designed specifically for frozen surfaces.
In the next section, we’ll go over how to successfully label frozen tubes, covering best practices and the specialized solutions that ensure labels stay in place and remain readable, even in ultra-low temperature storage.
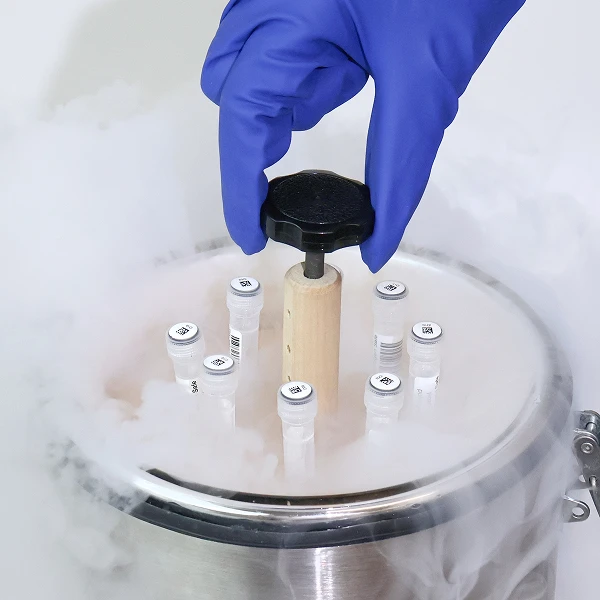
How to successfully label frozen cryovials.
Successfully labeling frozen tubes requires both the right method and the right materials. Even though frost, moisture, and extreme cold create challenges, it’s entirely possible to apply a secure, long-lasting label to a frozen tube—as long as you follow the correct steps. The key is to prepare the tube properly and use a label that’s specifically engineered to bond at frozen temperatures. Skipping either of these steps can lead to adhesion failure, label peeling, or unreadable barcodes, putting sample traceability at risk.
Step 1: Always Wipe the Tube Dry
Regardless of what label you use, removing frost and moisture is the first and most important step. Nothing sticks to water, and when a tube is pulled from a -80°C freezer, it immediately starts collecting condensation from the surrounding air. Even a label with a frozen-surface adhesive can’t form a strong bond if there’s a layer of frost between the adhesive and the tube. To ensure proper adhesion, use a lint-free wipe to remove all visible moisture before applying the label. This gives the adhesive direct contact with the tube’s surface, creating a secure, long-lasting bond that won’t weaken when the sample is returned to cryogenic storage.
Step 2: Choose the Right Label for Frozen Application
Most cryogenic labels, even those rated for -196°C storage, must be applied at warmer temperatures to bond properly. If a label isn’t formulated for direct frozen surface application, it will fail even if the tube is dry. That’s why it’s essential to use a label designed specifically to bond at ultra-low application temperatures. For frozen tube labeling, there are two primary solutions:
- Frozen Surfaces Cryo Label – Features an adhesive specifically engineered to bond to frozen surfaces, ensuring instant adhesion even at -80°C.
- Wrap-Around Tube Label – Uses a self-laminating design that adheres to both the tube and itself, adding extra security against peeling in extreme cold.
By following these steps, lab techs can successfully relabel frozen tubes without needing to thaw samples or risk losing track of critical specimens. In the next section, we’ll take a closer look at these two labeling solutions, explaining how each works and when to use them for the best results.
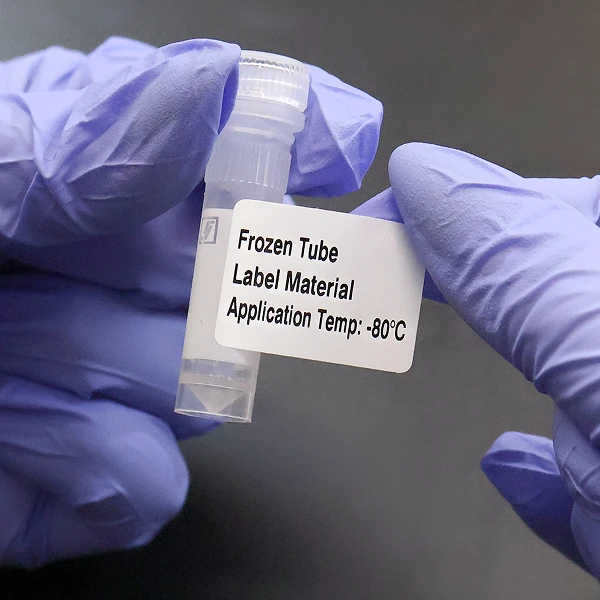
Solution 1: Frozen Surfaces Cryo Label
When a lab needs to relabel frozen tubes without thawing, the Frozen Surfaces Cryo Label is the best solution. Whether samples are being transferred from a biobank, reorganized for a new study, or relabeled due to barcode failure, this label allows lab techs to apply a secure, scannable label directly onto a frozen surface at -80°C. Standard cryogenic labels may be rated for ultra-low operating temperatures, but if they require a warmer application temperature, they won’t bond properly to a frozen tube. That’s why this label was specifically engineered with an adhesive that activates immediately at cryogenic temperatures, ensuring a strong, permanent bond as soon as it’s applied.
Unlike most cryo labels, which require the tube to be thawed before labeling, the Frozen Surfaces Cryo Label eliminates that extra step. It features a thin polyester face stock with an acrylic adhesive, designed to bond instantly to frozen tubes without weakening over time. Since the application temperature and operating temperature are the same, there’s no risk of delayed adhesion failure when the tube is placed back into cryogenic storage. Lab techs can apply it in one step and be confident that the label will remain secure through freeze-thaw cycles, handling, and long-term storage in -80°C freezers or liquid nitrogen (-196°C) environments.
Key advantages of the Frozen Surfaces Cryo Label
- Bonds instantly at -80°C
- No thawing required before application
- Acrylic adhesive engineered for frozen surfaces
- Permanent adhesion for long-term cryogenic storage
- Thin polyester face stock for durability
- Prevents misidentification and relabeling failures
For labs that frequently receive or reorganize frozen samples, this label offers a fast, effective solution without disrupting storage conditions. But in some cases, particularly for cryovials and small tubes, a wrap-around label may provide additional security by adhering to both the tube and itself. In the next section, we’ll explore how Wrap-Around Tube Labels work and when they are the best choice for labeling frozen samples.
Solution 2: Wrap-Around Tube Label
For cryovials and small tubes, a wrap-around label provides an extra layer of security, ensuring the label remains attached even in high-moisture, ultra-low-temperature environments. When relabeling frozen tubes, direct adhesion to a frozen surface can be challenging, but the Wrap-Around Tube Label solves this problem by adhering to itself. Instead of relying entirely on the bond between the adhesive and the tube, this label wraps completely around the vial, securing itself with a 360° laminate overwrap. This design locks the label in place, preventing peeling or lifting, even when stored in liquid nitrogen (-196°C) or ultra-low freezers (-80°C).
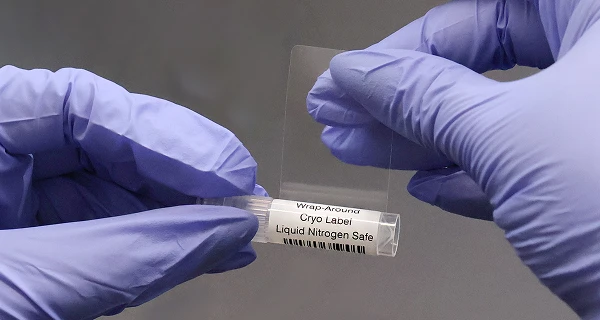
This label is made from a top-coated polypropylene face stock, offering excellent clarity, ink adhesion, and moisture resistance. The acrylic adhesive alone is not optimized for bonding directly to frozen surfaces, but because the label adheres to itself, it creates a tight, durable seal that remains secure even in cryogenic storage. The laminate overwrap adds extra protection, shielding printed information from frost, condensation, and physical handling while ensuring long-term barcode readability. This makes it an ideal solution for labs handling high-value samples that must remain perfectly labeled throughout storage and retrieval cycles.
Key advantages of the Wrap-Around Tube Label
- Self-sealing design adheres to itself for extra security
- 360° laminate overwrap protects printed information
- Resistant to moisture, frost, and liquid nitrogen conditions
- Top-coated polypropylene ensures excellent ink adhesion
- Durable and scannable for long-term cryogenic storage
- Ideal for cryovials and small-diameter tubes
For lab techs working with high-density cryo storage, where vials are handled frequently and exposed to moisture, this wrap-around design adds an extra layer of reliability. While the Frozen Surfaces Cryo Label is best for direct frozen application, this solution provides added durability for small-diameter tubes and high-handling environments.
Labeling frozen tubes is a common challenge in labs, but with the right approach and materials, it’s entirely possible to apply a secure, scannable label without thawing samples. Whether you’re reorganizing a collection, relabeling biobank samples, or replacing failed labels, using a standard cryo label won’t work unless it’s designed for frozen surfaces. The Frozen Surfaces Cryo Label is the best option for direct application to -80°C tubes, while the Wrap-Around Tube Label provides extra security for cryovials by sealing around itself. Both solutions ensure labels remain intact and readable through freeze-thaw cycles, handling, and long-term cryogenic storage.
If your lab needs a proven solution for labeling frozen tubes, we have both options available in our shop. Don’t let labeling challenges slow down your workflow—choose a label engineered to work in extreme cold.
Connect with our labelling experts today
Blog article form
"*" indicates required fields